By Lauren Nagel
The drone engineering process often operates as a ‘design loop’, which refers to the circular nature of the design process. Building the first version of the drone relies on certain assumptions, many of which will change as components are selected and the design comes together.
In this article we will cover:
- Finding a battery to increase flight time
- How to choose a drone motor and propeller (with database)
- Swapping components to maximize efficiency
- How to choose an ESC
- How to calculate drone flight time
We will be using the Series 1585 thrust stand to gather data for this article.
The design loop begins when the designer looks at how the first version of the design differs from the assumptions, then goes back to the beginning with the new information (figure 1).

Figure 1: The drone design loop illustrated
In our previous article, How to Increase a Drone's Flight Time and Lift Capacity, we covered the first stage of the design process and reached a first version of our design. In this article we will start where we left off, looking at how our assumptions held up.
Review
We started our design process with the assumption that our drone would weigh 777 g and would be able to fly on its own. Following these assumptions, we predicted we would need 1.9 N of thrust per propeller for hover flight, so we looked for the motor-propeller combination that would be most efficient at 1.9 N. Once we found the most efficient combination, we had the tools needed to estimate our flight time, which is where we will start off today.
For this article we will be more precise with the mass of our components. We will assume the following mass breakdown of our 777 g drone:
- Motors (4): 148 g
- Propellers (4): 13.5 g
- Battery (1): 155 g
- Other components (camera, frame, ESC, etc.): 460.5 g
Flight Time
Our goal is to maximize our drone’s flight time so that it can hover as long as possible. In our previous article, we modelled the flight time of our drone with varying battery capacity (figure 2).

Figure 2: Flight time vs. battery capacity for the original drone design
We presumed our design would include a Turnigy nano-tech 1300 mAh 4S battery and included its mass in our overall calculations. The battery’s capacity is just over 19.2 Wh (14.8 V * 1.3 Ah = 19.2 Wh), which occurs within the growth phase of the graph and gives us only about 4.5 minutes of flight time.
If we increased the battery capacity, we could also increase our flight time, but the trade off would be increased weight. This is where the design loop begins, as we swap components to try and build the drone that best meets our needs.
Iteration 2: Choosing a New Battery for Maximum Flight Time
Up to the 0.2 hour mark there is an increase in flight time with increased battery capacity, but after about 100 - 125 Wh the marginal gains become less significant. For this reason, we will start by swapping our old battery with a new battery that has around 100 - 125 Wh of capacity in order to increase our flight time. The Turnigy 5000mAh 6S LiPo pack nicely fits our criteria with 111 Wh of capacity (figure 3).

Figure 3: Turnigy 5000 mAh/ 111 Wh LiPo battery (Photo: HobbyKing)
This new battery weighs a whopping 655 g compared to our old battery that weighed just 155 g. Assuming all of our other components stay the same at 622 g, the total mass of our drone is now 1,277 g.
We will therefore need to produce at least 12.5 N of thrust for the drone to hover (1.277 kg * 9.81), just over 3.1 N per propeller. We would also like to achieve at least double that thrust to have a good control authority, so we will be looking for the propeller that is most efficient at 3.1 N, but can also achieve up to 6.2 N of thrust.
To review, we have three propellers in our list of candidates:
- 6030R Gemfan => diameter: 6", pitch: 3", mass 2.22 g
- 6040R King Kong => diameter: 6", pitch: 4", mass 3.38 g
- 5030R Gemfan => diameter: 5", pitch: 4", mass 3.00 g
We will work with the assumption that our drone frame is set and we cannot exceed 6” in diameter for our propellers. We can learn about our three propeller candidates by looking through the RCbenchmark database of electric motors, propellers and ESCs. Test data such as thrust, torque, RPM, power, efficiency and more is collected using one of our propulsion test stands, and for this drone the RCbenchmark Series 1585 would likely be the best fit.
For our candidates, data from the database tells us that all three propellers reach our hover thrust of 3.1 N, but only the 6040R King Kong nears the maximum thrust of 6.2 N (0.63 kgf) (figure 4).

Figure 4: Thrust performance of the propeller candidates
These results suggest that either our battery is too heavy or our motor/ propeller combination was not producing sufficient thrust. We are aiming to have the longest flight time possible, so rather than looking for a smaller battery right away, let’s explore some more propellers that fit within our frame limits, but produce more thrust.
Further reading: How Imbalance Causes Propeller Vibration
Iteration 3: Choosing New Propeller and Motor Candidates
Our frame limits us to propellers that are 6” or less in diameter, but we can still experiment with our pitch, material, and brand. We will use the drone component database to filter for propellers that are 6” in diameter and produce at least 6.2 N (0.63 kgf) of force. This search provided several good options, but for simplicity we will narrow it down to three candidates that produce the most thrust:
- Propeller 1 → diameter: 6”, pitch: 4”, mass: 3.38 g, material: plastic
- Propeller 2 → diameter: 6”, pitch: 4”, mass: 4.32 g, material: nylon
- Propeller 3 → diameter: 6”, pitch: 4.5”, mass: 6.78 g, material: carbon fiber (CF)
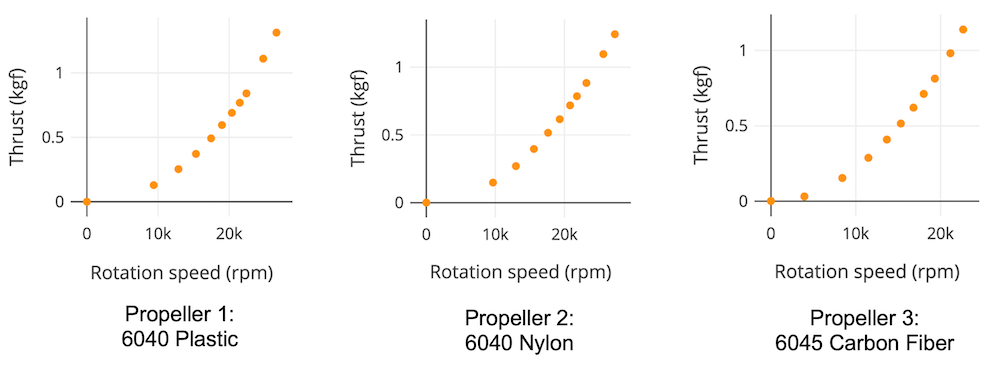
Figure 5: Thrust vs. RPM for the new propeller candidates
As you can see in figure 5, all of our propeller candidates can produce 10 N (1 kgf) of thrust or more. For this reason, we can aim for a hover thrust of 5 N and a max thrust of 10 N, which will allow us to lift a larger battery with the same propulsion unit.
As shown in figure 6, at our original hover thrust of 3.1 N (0.32 kgf) and at our new hover thrust of 5.0 N (0.51 kgf) the efficiency of propeller 1 and propeller 2 is very similar, separated by only about 0.1 gf/W. Propeller 2 is slightly more efficient, but it is also heavier. This increased weight could lead to a shorter flight time and leaves less mass available for the battery. In a quadcopter, the total difference would be 3.76 g ((4.32 g - 3.38 g)*4).

Figure 6: Propeller efficiency vs. thrust for the new propeller candidates
After a quick look at the online marketplaces, it is evident that 4g makes no difference in terms of capacity for batteries of this size. For this reason, and the negligible effect of 4 g of mass for our drone, it makes sense to use propeller 2 due to its higher efficiency.
Our next step will be to find the brushless motor that is most efficient with this propeller at our new hover thrust of 5 N. In general, we are looking for a motor that can exceed our max thrust of 10 N, but not by too large a margin. We don’t want to operate the motor at its maximum speed for too long, but we also don’t want to haul a motor that produces more thrust and torque than we need.
Of the two motors we tested previously, MultiStar Elite 2306 2150 Kv and EMAX RSII 2207 2300 Kv, only the 2300 Kv motor meets our max thrust requirement (figure 7). We will therefore have to use the motor database to find a new candidate.

Figure 7: Motor efficiency vs. thrust for 2150 Kv and 2300 Kv motor candidates
From the database we find the Hypetrain Blaster 2207 2450 Kv, which meets our criteria. We ran a test with each of the two motors paired with propeller 2, and the results are shown in figure 8. Motor 2, EMAX RSII 2207 2300 Kv, is the most efficient with propeller 2 at our hover operating point of 5 N (0.51 kgf) and it also happens to be more efficient at our max thrust of 10 N (1.02 kgf). The efficiency difference at hover thrust is about 2.2% (55.6% vs. 53.4%), but the 2300 Kv motor is also lighter (32.37 g vs. 36.96 g), so it makes our decision easy.

Figure 8: Motor efficiency vs. thrust for 2300 Kv and 2450 Kv motor candidates
Iteration 4: Choosing a New Battery for Maximum Flight Time That Fits Our New Design
Now is a good time to summarize the mass of our components since the mass of our propellers and motors has changed as well as our hover thrust. Here is the new breakdown:
- Motors (4): 129.5 g
- Propellers (4): 17.3 g
- Other components (camera, frame, ESC, etc.): 460.5 g
- Pre battery mass: 607.3 g
- Max mass: ~ 2,000 g
Based on these new values, we have 1392.7 g of mass available for our battery.
Since we also have our motor and propeller picked out, we can also determine our discharge (C rating) needs, which will also be a consideration for picking out the battery. We want to be sure that our motor will not draw more current than our battery can provide, or else the battery could rapidly degrade or overheat. The formula for determining current draw for a battery is: Current (A) = C rating * Capacity (Ah).
Further reading: Brushless Motor Power and Efficiency Analysis
There is no information on continuous or burst current for the EMAX RSII 2207 2300 Kv online, but we can look at data in the RCbenchmark database and compare all tests done with this motor. As we can see in figure 9, the max current reached during various tests was about 42 A.

Figure 9: Current vs. Rotation speed for EMAX RSII 2207 2300 Kv motor
The Turnigy High Capacity 16000 mAh 4S 12C Lipo Pack has the highest capacity in Wh of all the batteries in our weight range, giving us 4 * 3.7 * 16 = 236.8 Wh. It weighs 1,366 g, has a 12 C discharge rating and 16 Ah of capacity, so it can handle a current draw of 192 A, which is more than we need.
Iteration 5: Choosing an ESC
The main consideration for choosing an ESC is that it can deliver the motor’s peak current. In our case we do not expect our motor to exceed 42 A, so an ESC like the HobbyKing 60A ESC 4A SBEC will work great. It can deliver a constant current up to 60 A and a burst current up to 80 A, while providing 4 A to the BEC. This gives us a bit of a safety margin, so this ESC will be a good choice for our drone.

Figure 10: HobbyKing 60A ESC 4A SBEC (Photo: HobbyKing)
Calculating Our Flight Time
As we learned in our previous article, flight time is dependent on the capacity of the battery and the power drawn by the propulsion system. Many factors thus come in to play, summarized in the formula below (see previous article on increasing flight time for more details):
Where
E = capacity
σ = energy density
M = mass in grams (g)
We can copy+paste our propulsion test data into this handy flight time calculator, plug in our weight and battery capacity, and it will give us the best estimate of our flight time based on our data. Our estimated flight time is 15.2 minutes (figure 11), which is a significant improvement compared to our original design, which had only about 4.5 minutes of flight time.

Figure 11: Using the flight time calculator to estimate our drone’s flight time
Conclusion
As we have seen, the drone design process is cyclical and there’s almost always room to improve a design.
If you want to take your design a step further, consider adding custom sensors to your test setup.
Collecting propulsion data is one of the best ways to determine where there is room for improvement in your drone, and we offer many test stands and tools to help you do so:
- Series 1585 - measures up to 5 kgf of thrust / 2 Nm of torque
- Flight Stand 15 - measures up to 15 kgf of thrust / 8 Nm of torque
- Flight Stand 50 - measures up to 50 kgf of thrust / 30 Nm of torque
- Flight Stand 150 - measures up to 150 kgf of thrust / 150 Nm of torque
If you enjoyed this article, you will also enjoy our free eBook: Drone Building and Optimization: How to How to Increase Your Flight Time, Payload and Overall Efficiency.
Nadeeka Rathnayake
September 23, 2024
👍